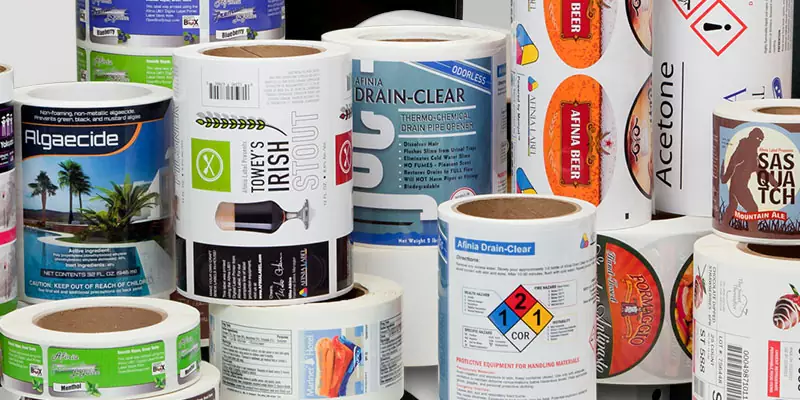
Label printing might seem a minor detail in product presentation, but it holds substantial importance in conveying brand essence and product information. Professional-looking labels elevate your product’s appeal, drawing attention and imparting credibility. In this guide, we’ll delve into twelve essential tips to empower your DIY label printing journey, enabling you to create labels that are both aesthetic and informative.
Table of Contents
Know Your Purpose
Source: drinkpreneur.com
Understanding the primary aim of your label is the first step in creating effective labels. The purpose guides the design, size, and placement of the label, whether it’s a vibrant product label or a simplistic address label. For instance, product labels should be compelling and reflective of the brand, whereas address labels require clarity and accuracy. Knowing your label’s role aids in deciding the content, design, and material, ensuring it serves its intended function optimally.
Different Purposes, Different Labels
Let’s consider a cosmetic product label. It should be visually appealing, incorporate brand colors, logos, and possibly, illustrative elements to attract customers. Conversely, address labels necessitate legibility over intricate designs, focusing on clear fonts and accurate information.
Choose the Right Label Material
Material choice is pivotal, impacting the label’s appearance, durability, and adherence. Popular materials include paper, vinyl, and transparent ones, each serving distinct purposes. For example, paper labels are versatile but may lack durability, whereas vinyl labels are resilient but might be overkill for simple applications. Transparent labels offer a sleek look, blending with the product seamlessly. The key is to align the material with the label’s purpose and a label printer, considering factors like exposure to elements, required durability, and desired aesthetic.
Material Matters
The material’s texture and finish can augment or diminish the label’s overall appearance. A matte finish might suit a minimalist, modern one, while a glossy finish can enhance vibrant colors. Understanding the synergy between material and design is crucial in crafting a cohesive and appealing label.
Design Tips
Source: canva.com
Good design is the linchpin of effective labeling. It encapsulates color schemes, font choices, and branding consistency. A harmonious color palette and legible fonts are foundational in creating visually pleasing labels. Maintaining brand consistency across it reinforces brand identity, fostering recognition and trust.
Crafting Eye-catching Designs
Experimenting with color contrasts, font weights, and sizes can yield dynamic and attention-grabbing labels. Leveraging design software can aid in experimenting with different design elements, allowing you to visualize the final product effectively. Balancing creativity with coherence is paramount in devising designs that are both unique and informative.
Use High-Quality Images and Graphics
High-resolution images and graphics are non-negotiable in professional label printing. They ensure clarity and detail, avoiding pixelation and blurriness. Sourcing images from reputable stock photo sites or creating custom graphics can enhance its quality significantly.
Proper Image Placement
Strategically placing images can optimize label aesthetics and information conveyance. Considering image proportions and maintaining a balance between text and imagery ensure that it is cohesive and informative.
Label Size and Shape
The size and shape of your label play a pivotal role in its overall appearance and impact. Choosing appropriate dimensions, considering the product’s size and shape, ensures that it complements rather than overshadows the product.
Unconventional Shapes
Exploring unconventional shapes can add a unique flair to your labels. However, unconventional should not compromise the label’s readability and adherence. Assessing the product and experimenting with different shapes can help in finding the perfect match.
Printing Technology Options
Source: pcforms.com
Different DIY printing technologies like inkjet, laser, and thermal offer varied results. Inkjet printers excel in color vibrancy, while laser printers provide sharp text and graphics. Thermal printers are ideal for high-volume label printing due to their speed and efficiency. Assessing your label needs and understanding the capabilities of each technology are essential in choosing the right printer.
Pros and Cons of Technologies
Weighing the advantages and disadvantages of each technology based on print quality, speed, and cost can guide your decision-making process, aligning your choice with your project’s specific requirements.
Calibration and Test Printing
Calibration is crucial in achieving accurate color reproduction and alignment. Regular calibration and test printing allow you to make necessary adjustments before the final print, ensuring optimal results.
Troubleshooting Solutions
Identifying common issues like color discrepancies and alignment errors during test printing can save time and resources. Having a troubleshooting guide handy can streamline the adjustment process, enhancing print accuracy and quality.
Consider Label Finishing Options
Label finishing like lamination and varnishing can elevate your label’s appearance and durability. These finishing options add a protective layer, enhancing resistance to elements and wear. Considering these options, especially for labels exposed to harsh conditions, can prolong its life and maintain aesthetic appeal.
When to Consider Finishing
Evaluating the exposure and durability requirements of your labels can help in deciding whether to opt for finishing options, balancing additional costs with benefits.
Label Application and Placement
Source: labels-u-print.com
Applying labels evenly and straight is integral in maintaining a professional appearance. Proper placement enhances product presentation, ensuring that the label serves its intended purpose effectively.
Tips for Reapplication
In case of misapplication, having a method to remove and reapply labels without damaging them or the product is valuable in maintaining label integrity and appearance.
Quality Control and Proofreading
Quality control is paramount in DIY label printing. Proofreading and error-checking processes are essential steps in avoiding common mistakes like typos and misalignments, ensuring that the label is flawless and professional.
Common Mistakes to Avoid
Being vigilant about potential errors and having a checklist for common mistakes can aid in producing error-free labels, maintaining a high standard of quality.
Sustainability and Eco-Friendly Options
Embracing eco-friendly materials and printing practices not only contributes to environmental conservation but also appeals to eco-conscious consumers. Exploring recycling options and sustainable disposal methods is a responsible practice, aligning your labeling efforts with environmental stewardship.
Making Conscious Choices
Choosing sustainable materials and reducing waste by optimizing label sizes and layouts are practical steps in creating eco-friendly labels, reflecting a commitment to sustainability.
Conclusion
Creating professional-looking labels is an art, blending creativity, precision, and attention to detail. By understanding your label’s purpose, choosing appropriate materials and designs, employing high-quality images, and considering sustainability, you can craft labels that resonate with consumers and elevate your product presentation. So, embark on your DIY label printing journey with confidence, armed with these comprehensive insights, and make every label a masterpiece.