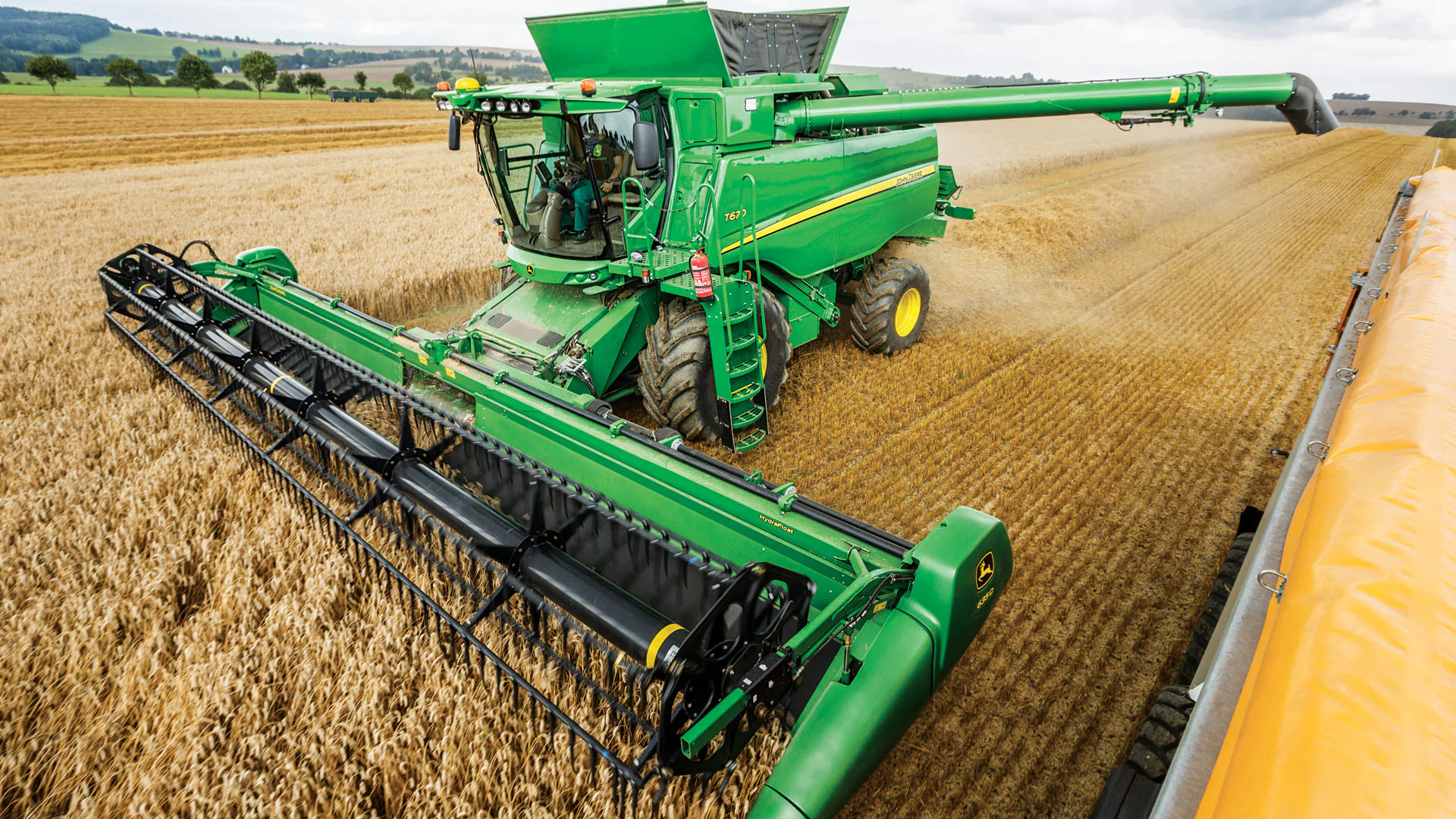
In the agricultural industry, the phrase “time is money” is more than a cliché; it is a fundamental truth. Efficiency, productivity, and equipment reliability directly influence a farmer’s bottom line. Central to this is the harvester, a cornerstone of modern farming.
More specifically, the effectiveness of combine equipment can make or break a successful harvest season. This article delves into the critical role that harvester replacement parts play in maximizing yield, focusing on how timely maintenance and part replacement can significantly impact crop harvesting.
Table of Contents
Understanding the Combine Harvester
The combine harvester, commonly known simply as a combine, is a versatile machine designed to efficiently harvest a variety of grain crops. The name derives from its ability to combine three separate harvesting operations—reaping, threshing, and winnowing—into a single process. This machinery is essential for crops such as wheat, oats, rye, barley, corn, soybeans, and more. Given its importance, maintaining the efficiency and functionality of a combine harvester is paramount.
The Importance of Harvester Replacement Parts
Source: 3dhorse.com
Enhanced Performance
Replacement parts are crucial for maintaining a combine harvester’s optimal performance. Over time, components like cutting blades, belts, chains, and gears wear out due to the immense workload they endure.
Using high-quality replacement parts ensures that the combine operates at peak efficiency, which directly translates to better crop yield. For instance, sharp cutting blades make cleaner cuts, reducing grain loss and ensuring that more of the crop is collected.
Reducing Downtime
Agricultural seasons are short and often dictated by weather conditions. Any downtime during the harvesting season can lead to significant losses. Proactively replacing worn-out parts reduces the risk of unexpected breakdowns.
This proactive approach helps in maintaining a continuous workflow, ensuring that the harvest is completed within the optimal time frame. In the context of combined equipment, downtime not only affects yield but can also impact the quality of the harvested crops.
Cost Efficiency
While it might seem counterintuitive, investing in replacement parts can be cost-efficient in the long run. Neglecting the maintenance of a combine harvester can lead to more severe mechanical failures, resulting in expensive repairs or even the need for a complete replacement.
By regularly updating and maintaining parts, farmers can avoid these hefty costs and extend the lifespan of their equipment. Additionally, well-maintained equipment often consumes less fuel and operates more efficiently, further saving costs.
Safety
A well-maintained combine harvester is a safer machine to operate. Faulty parts can lead to accidents, which can cause injuries and further downtime. Ensuring that all parts are in good working condition minimizes the risk of accidents, creating a safer working environment for the operators.
Key Replacement Parts for Combine Harvesters
Source: deere.com.au
Cutting Blades and Sections
The cutting system of a combine harvester is critical for efficient crop collection. Blunt or damaged blades can lead to uneven cuts, leaving behind a significant portion of the crop. Regular inspection and replacement of cutting blades and sections ensure clean and precise cutting, maximizing the amount of crop harvested.
Belts and Chains
Belts and chains are essential for the movement of various parts within the combine. They transfer power from the engine to different components, such as the threshing drum and the conveyor. Worn-out belts and chains can slip or break, leading to significant downtime. Regular replacement of these components ensures smooth operation and prevents sudden breakdowns.
Threshing Components
The threshing mechanism separates the grain from the chaff. This process is crucial for the quality of the harvested crop. Worn-out threshing bars or concaves can lead to inefficient separation, resulting in grain loss. Replacing these parts as they wear out ensures effective threshing and improves the overall quality of the harvest.
Sieves and Screens
Sieves and screens play a vital role in cleaning the grain before it is stored. Over time, these components can become clogged or damaged, reducing their effectiveness. Regular maintenance and replacement of sieves and screens ensure that the grain is properly cleaned, reducing the amount of foreign material in the final product.
Bearings and Bushings
Bearings and bushings facilitate the smooth operation of rotating parts. When these components wear out, they can cause increased friction and heat, leading to potential mechanical failures. Replacing bearings and bushings as part of routine maintenance ensures that all moving parts operate smoothly, reducing wear and tear on other components.
The Impact of Technological Advancements
Source: farmprogress.com
The role of harvester replacement parts in maximizing yield has been further enhanced by technological advancements. Modern combine equipment now features advanced monitoring systems that alert operators to potential issues before they lead to significant problems. These systems can detect wear and tear on parts, allowing for timely replacements and reducing the risk of unexpected breakdowns.
Precision Agriculture
Precision agriculture has revolutionized the farming industry, and combine harvesters are at the forefront of this transformation. GPS technology, sensors, and data analytics enable farmers to monitor the performance of their equipment in real time. For instance, sensors can detect when a cutting blade is becoming dull and needs replacement. This level of precision ensures that replacement parts are used effectively, maximizing yield and efficiency.
Automation and Robotics
Automation and robotics are also making their way into combined equipment. Automated systems can perform routine maintenance tasks, such as lubricating moving parts and adjusting settings for optimal performance. These advancements reduce the reliance on manual labor and ensure that maintenance is performed consistently and accurately.
Best Practices for Maintenance and Replacement
Source: estesperformanceconcaves.com
Regular Inspections
Regular inspections are the cornerstone of effective maintenance. Farmers should establish a routine inspection schedule to check the condition of all critical components. This proactive approach allows for early detection of wear and tear, ensuring that replacement parts are ordered and installed before a breakdown occurs.
Quality Parts
Investing in high-quality replacement parts is crucial. While cheaper parts might seem like a cost-saving measure, they often wear out faster and can lead to more frequent breakdowns. High-quality parts from reputable manufacturers offer better durability and performance, ultimately saving money in the long run.
Training and Education
Operators should be well-trained in the maintenance and operation of combine harvesters. Understanding how to recognize signs of wear and tear and perform basic maintenance tasks can significantly extend the equipment’s lifespan. Continuous education on the latest advancements in combining technology and maintenance practices is also beneficial.
Documentation and Record-Keeping
Keeping detailed records of maintenance activities and replacement parts is essential. This documentation helps track the equipment’s performance and identify patterns of wear and tear. It also assists in planning future maintenance activities and budgeting for replacement parts.
Case Study ─ Successful Implementation
Source: farmprogress.com
To illustrate the impact of proper maintenance and replacement of harvester parts, let’s consider a case study of a mid-sized grain farm in the Midwest. The farm had been experiencing frequent downtime during the harvest season due to equipment failures. After consulting with agricultural engineers, the farm implemented a comprehensive maintenance plan that included regular inspections and the use of high-quality replacement parts.
Results
- Reduced downtime ─ The farm saw a 50% reduction in downtime during the harvest season. This improvement allowed the farm to complete the harvest more efficiently, avoiding losses due to weather-related delays.
- Increased yield ─ With the combine harvester operating at peak efficiency, the farm reported a 10% increase in yield. The cleaner cuts and better threshing improved the overall quality and quantity of the harvested crop.
- Cost savings ─ While the initial investment in high-quality parts was higher, the farm saved money in the long run by avoiding costly repairs and reducing fuel consumption. The extended lifespan of the combine harvester also deferred the need for a new purchase.
- Improved safety ─ The proactive maintenance plan reduced the risk of accidents, creating a safer working environment for the farm’s operators.
Conclusion
Maximizing yield in crop harvesting is a multifaceted challenge that hinges on the efficiency and reliability of combine equipment. Harvester replacement parts play a critical role in this equation, impacting everything from performance and downtime to cost efficiency and safety.
By investing in high-quality parts, implementing regular maintenance schedules, and leveraging technological advancements, farmers can ensure their combines operate at peak efficiency. This proactive approach not only maximizes yield but also enhances the overall sustainability and profitability of the farming operation. In the fast-paced world of agriculture, where every moment counts, the importance of well-maintained and efficient combine harvesters cannot be overstated.