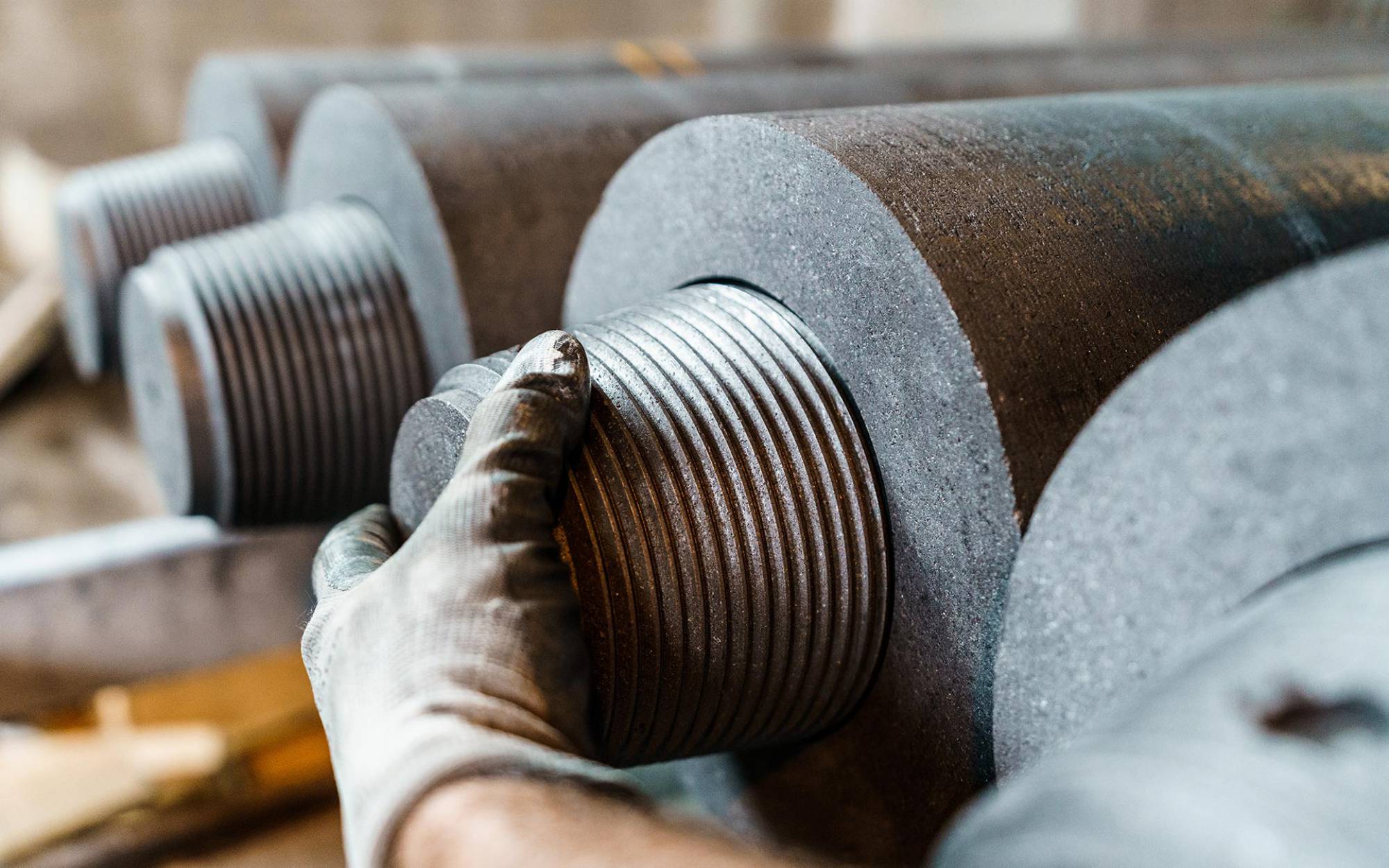
Are you looking for a graphite electrode that can provide enhanced performance and last longer? Choosing the right type of graphite electrode for your application is essential to ensure optimal performance. You need to consider various criteria like material properties, size, shape, and porosity to ensure you find the best solution for your needs.
Graphite electrodes are important components in modern steel mills. Used during the Electric Arc Furnace (EAF) process, they help conduct high levels of heat, energy, and electrical current while still being able to withstand extreme temperatures.
It is also important to note that not all graphite electrodes are suitable for use with every furnace or system—different types need different combinations of grade, size, and number of electrodes to function optimally in specific applications. It is crucial that correct advice from Chinese graphite electrode manufacturers is sought prior to making any purchasing decisions for the best result.
Table of Contents
Understanding Graphite Electrodes
Source: japanchemicaldaily.com
Graphite electrodes are a key component of electric arc furnace steel production, the process by which scrap steel and iron ore are melted together to create new steel products. They work by allowing an electric current to flow between the electrode and the steel bath, generating a tremendous amount of heat that can reach over 3,000° Celsius. In order for the graphite electrodes to perform optimally, it is essential that they are correctly selected for the specific application.
Types of Graphite Electrodes
These electrodes are composed of a network of graphite particles that are bonded together by a bonding matrix. The choice of the type of graphite electrode will depend on its purpose as different graphite electrodes undergo different manufacturing processes and thus vary in their properties and characteristics. The following is an overview of the three most common types of graphite electrodes available—regular power, high power, and ultra-high power—as well as their key differences.
Regular Power Electrodes
These offer good levels of conductivity and arc stability. They are typically used in primary steel production or in electric arc furnace operations where thermal stresses are moderate and long electrode life is important. This type of electrode features a medium oxidation resistivity, which means it can be used at moderate temperatures without incurring too much wear or damage over time.
High-Power Graphite Electrodes
High-Power Electrodes have a higher oxidation resistivity and offer enhanced electrical conductivity for applications such as ladle refining or vacuum degassing with short electrode lives. They also have very good mechanical properties and arc stability, making them ideally suited for continuous welding applications with extreme thermal stress conditions.
Ultra-High Power Graphites
They feature the highest levels of electrical conductivity and oxidation resistivities ever achieved in this industry. They feature longer lives than regular or high power, yet remain tough enough to withstand tough working conditions such as those found in secondary steel plants like bottom blasting furnaces or submerged arc furnaces where sparks reign all day long!
Factors to Consider
Source: cnbm2007.en.made-in-china.com
When choosing a graphite electrode for its electrical properties, the electrical resistance or resistivity of the material is a primary consideration. The tendency for electrons to pass through a certain material depends on its resistivity – which measures its “resistance” or opposition to electrical current flow.
They vary widely in terms of electrical resistivity, with some possessing values that are as low as 10-9 Ohm-m and others with values as high as 10-6 Ohm-m. Thus, it is important to know how much current is required in an application before selecting an appropriate type of graphite electrode.
Apart from its electrical properties, two other important factors that need consideration when selecting graphite electrodes are thermal conductivity and coefficient of thermal expansion (CTE).
Thermal conductivity determines how efficiently heat is conducted away from the area where it is produced while CTE refers to how much an object will expand or contract when exposed to changes in temperature. Graphite materials also possess varying levels of CTE; with lower CTE rates generally leading to greater stability over wide temperature ranges. Additionally, some types of specialized materials are tailor-made for low expansion or have been developed with additives that increase their thermal tolerances and capabilities even further.
Finally, when working with graphite materials it’s important to ensure proper machining practices – including surface finish requirements – is taken into account prior to commencing work. This can help ensure that during cutting operations, particles generated by adjacent areas will not be transferred onto the sensitive surfaces being machined through the use of cutting fluids or other methods such as cryogenic machining techniques.
Why are they widely used?
Source: lmmgroupcn.com
Graphites’ ability to resist corrosion and oxidation in high-temperature environments makes them an ideal choice for furnace applications. In addition, graphite electrodes offer excellent electrical conductance, and superior thermal shock resistance, and are easy to handle due to their low weight. Graphite is also a cost-effective material in comparison with alternative electrode types such as copper or aluminum.
The material offers several grades of hardness that can be tailored to suit various levels of wear resistance or compression strength. This makes graphite an excellent choice for applications where arcing is present as the higher grades of hardness offer better protection against arc erosion than softer materials do. Additionally, graphite’s excellent machinability allows it to be customized very effectively in order to achieve desired shapes or configurations that are required by certain designs.
Conclusion
When selecting the appropriate type of graphite electrode for your application, there are many factors to consider. First, you must take into account the operating conditions such as temperature and pressure. Additionally, you should consider the desired performance characteristics of the electrode, including potential impregnation materials, electrical resistivity, and strength after oxidation and thermal shock. Each application should be evaluated separately to determine the best type of graphite electrode based on these criteria.
Graphite electrodes can provide a wide range of benefits depending on their material properties and applied usage. As such, it is important to select the right type of electrodes for each application in order to maximize efficiency and performance.